Triple-Checking and turn on!
All power supplies are now installed. I checked all the connections and stride across the wall with a digital multimeter. After correcting some mistakes I turned on one supply after the other. It was a very crumbly feeling I must say, even after investing a lot of time to ensure that all connections were right.
Finally it works but the failing LED’s are still a topic. Here some pictures running on the development system. 3D functionality is not there yet. Also the planned foot switches to freeze and save the image are not installed yet.
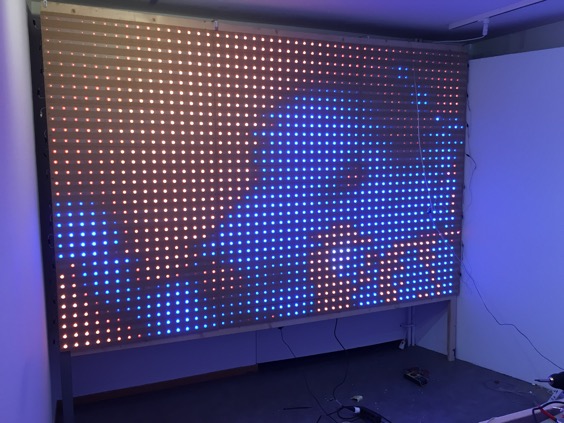
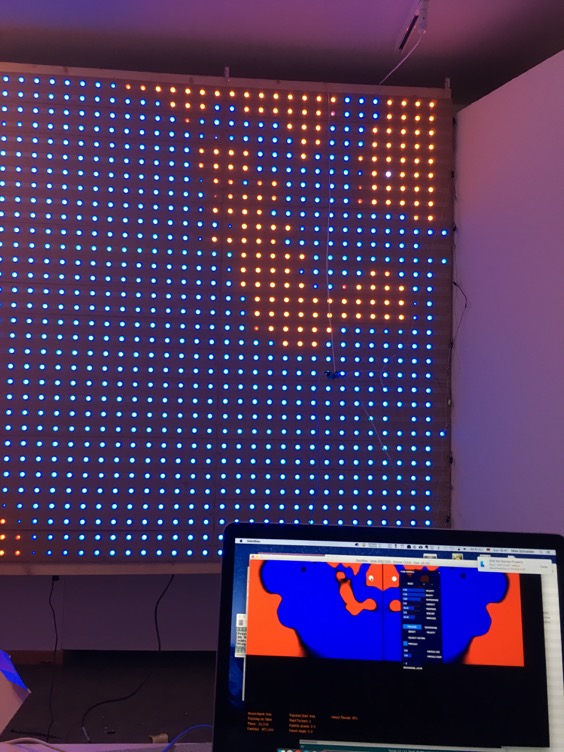